فولاد یکی از اصلی ترین متریال برای تولید محصولات مختلف در صنعت میباشد. روش های مختلفی برای تولید این ماده وجود دارد که هر کدام مزایا و معایب خاص خود را دارند. کوره قوس الکتریکی و القایی دو روش مرسوم برای تولید فولاد میباشند. در این مطلب از فولاد رامیار صنعت قصد داریم به بررسی تفاوت کوره القایی و قوس الکتریکی و تفاوت شمش قوس و القایی به صورت کامل بپردازیم.
مزایا و معایب کوره های القایی چیست؟
همانطور که گفتیم فولاد و شمش فولادی به دو روش کوره القایی و الکتریکی تولید و به بازار عرضه میشوند. این روش ها هر کدام مزایا و معایب خاص خود را دارند. در ادامه به بررسی مزایا و معایب کورههای القایی میپردازیم.
مزایای کوره القایی
- راندمان حرارتی بالا و انجام فرایند ذوب در کمترین زمان ممکن؛
- توزیع یکنواخت حرارت در سراسر مواد در حال ذوب؛
- عدم آلودگی صوتی در حین انجام عملیات ذوب؛
- استفاده در اتمسفر خنثی یا حتی خلا؛
معایب کوره القایی
- در کوره القایی فرکانس های متوسط و بالایی اعمال می شود؛ همین مسئله سبب افزایش قیمت آن میشود.
- تلاطم و سرد شدن مواد در سطح فوقانی، سبب میشود که سرباره برای تصفیه مذاب ممکن نباشد. در نتیجه از این کوره برای ذوب آلیاژ هایی که نیازی به تصفیه ندارند، استفاده میکنند.
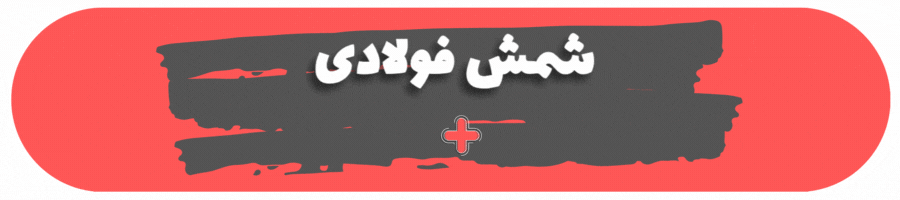
کاربرد کوره های القایی چیست؟
در ابتدا به بررسی مزایا و معایب کوره های القایی به صورت کامل پرداختیم. اما کاربرد این کوره ها در صنایع ذوب فولاد چیست؟ در ادامه به برخی از مهم ترین کاربردهای این نوع کوره اشاره خواهیم کرد:
- بهترین نوع کوره برای ذوب انواع فلزات رنگی است که به سبب عدم اکسیداسیون مذاب آلومینیوم، گرما و حرارت را به طور یکنواخت به فلزات منتقل میکند.
- کیفیت ذوب فلزات در کوره القایی بسیار بالا است و در نتیجه آلیاژ سازی به بهترین شکل ممکن انجام میشود.
- از این نوع کوره می توان حتی برای بازیافت قراضه های فلزی مثل آلومینیوم نیز استفاده کرد.
- به کمک کوره القایی، عملیات ذوب و ریخته گری در بالاترین سطح کیفی انجام میشود.
- کوره القایی برای ذوب کردن فلزات کمیاب بهترین انتخاب خواهد بود.
مزایا و معایب کوره قوس الکتریکی چیست؟
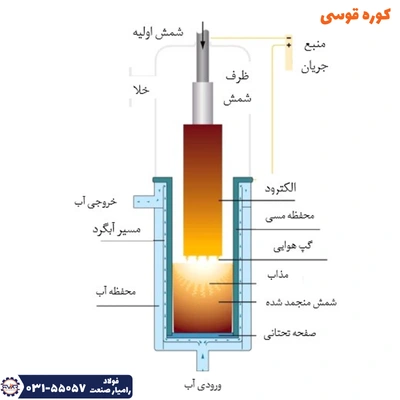
مزایای کوره قوس الکتریکی
- به دلیل دمای بسیار بالا، توانایی ذوب آلیاژهای نسوز را نیز دارد؛
- امکان بازیافت به منظور استفاده مجدد از عناصر آلیاژ فولاد؛
- امکان کنترل دمای کوره به بهترین شکل ممکن؛
- استفاده از قراضه به عنوان مواد اولیه؛
معایب استفاده از کوره قوس الکتریکی
- به سبب استفاده از قراضه، ناخالصی بیشتری به فولاد وارد میکند؛
- کیفیت فولاد به سبب استفاده از قراضه تحت تاثیر قرار میگیرد؛
- مدت زمان ذوب طولانی بوده و در نتیجه مصرف برق بالاتر است؛
- آلودگی صوتی بیشتری دارد؛
کاربرد کوره قوس الکتریکی
همانطور که در بخش مزایای کوره قوس الکتریکی گفتیم، این نوع کوره راندمان حرارتی بسیار بالایی داشته و 30 درصد از فولادهای جهان از طریق این کوره تولید میشوند. به همین دلیل از کوره قوس الکتریکی به صورت گسترده برای تولید میله، میلگرد، ناودانی، تسمه و حتی صنعت خودروسازی استفاده میشود.
تفاوت شمش قوس و القایی
تفاوت شمش قوس الکتریکی و کوره القایی در بازدهی عناصر آلیاژ
یکی از دیگر از تفاوت شمش قوس الکتریکی و کوره القایی در بازدهی عناصر آلیاژ است. سرباره در قوس الکتریکی گرم است و عناصر آلیاژی موجود در سرباره، اکسید شده و بعد از سرباره به فولاد مذاب بر می گردند. به سبب سوختن بیشتر عناصر آلیاژی در قوس الکتریکی، بازدهی عناصر آلیاژی در کوره های القایی بیشتر است.
در کوره القایی از کاربید سیلیسیم پر عیار برای تنظیم ترکیب شیمیایی استفاده میکنند. در نتیجه هزینه آلیاژ ها و مواد افزودنی غیر فلزی در در این دو روش متفاوت است. کیفیت ذوب تولید شده در کوره قوس بالاتر از القایی میباشد. همین مسئله سبب افزایش کیفیت شمش قوسی نسبت به القایی شده است. در بسیاری از مواقع از این نوع کوره برای بازیافت ضایعات فلزی مثل آلومینیوم استفاده میکنند.
تفاوت شمش قوس الکتریکی و کوره القایی از نظر نیروی انسانی
تعداد نیروهای انسانی لازم برای تولید شمش فولادی به روش قوس و القایی تقریبا یکسان است. در تولید شمش قوس الکتریکی حداقل 4 نفر و برای تولید شمش القایی به 5 نیروی انسانی نیاز داریم.
برای مطالعه بیشتر در مورد شمش فولادی، به صفحه " شمش فولادی چیست؟ " مراجعه کنید.
فرق شمش قوس الکتریکی و کوره القایی در بهره وری
میزان سوختن عناصر آلیاژی در کوره قوس بیشتر از القایی است. همچنین کیفیت ذوب در کوره قوس الکتریکی بالاتر از القایی میباشد. همین ویژگی سبب شده است تا فرایند آلیاژسازی با کیفیت بالاتری انجام شود و آلیاژ های نسوز نیز تحت تاثیر حرارت ذوب شوند. با توجه به آنچه گفته شد، از آنجاییکه در کوره قوس، حتی آلیاژ های نسوز هم ذوب میشود، شمش فولادی تولید شده دارای ناخالصی بیشتری میباشد.
فرق شمش القایی و قوس الکتریکی در دفع گرد و غبار
یکی دیگر از تفاوت های شمش قوس الکتریکی و القایی این است که گرد و غبار تولید شده از کوره القایی به صورت مجدد قابل استفاده است. لازم به ذکر است که گرد و غبار کوره القایی حدود 1 درصد نسبت به کوره قوس الکتریکی کمتر میباشد.
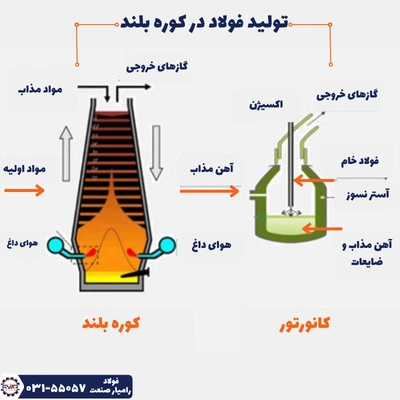
فرق شمش قوسی و القایی از نظر ترمودینامیکی
فرق شمش قوسی و القایی از نظر ترمودینامیکی نیز میباشد. در کوره القایی دما و حرارت، زمان تصفیه، قدرت هم زدن و همچنین حفظ درجه حرارت بسیار راحت تر از شمش قوس الکتریکی است. شرایط ترمودینامیکی و جنبشی در کوره القایی سبب شده است تا همگن سازی مواد مذاب و ترکیب فولاد بهتر انجام شود.
فرق شمش قوس الکتریکی و کوره القایی در تصفیه
از تفاوت های شمش قوس و القایی از نظر تصفیه می توان به موارد زیر اشاره کرد:
- در تولید شمش القایی از کربن خالص به صورت گرافیت برای کربن دهی استفاده میکنند. در نتیجه برای ذوب بار فلز به کربن دهی نیاز است. این در حالیست که در شمش قوسی، از یک الکترود سنگی استفاده میکنند.
- سرباره کوره القایی سرد بوده و میزان نیتروژن آن کمتر و اکسیژن بیشتری نسبت به قوس الکتریکی دارد. این مسئله سبب شده است تا اکسیژن در کوره القایی کنترل نشده و فروآلیاژ ایجاد شود.
- فسفر و گوگرد زدایی در شرایط مختلف انجام می شود. در صورت بالا بودن این دو عنصر در ذوب، امکان پایین آوردن آنها در روش القایی دشوار تر است.
- قوس الکتریکی سرباره گرم تولید میکند و در رفع اکسیداسیون قوی تر عمل میکند. در نتیجه فسفر و گوگرد را سریعتر جذب خواهد کرد.
تفاوت شمش قوسی و القایی در مصرف برق
میزان مصرف برق در کوره القایی بالاتر از قوس الکتریکی است. در کوره قوس الکتریکی به واسطه ورود انرژی شیمیایی با اکسیژن، زمان روشن بودن آن کمتر از کوره القایی میباشد. همین مسئله سبب کاهش مصرف برق در کوره قوسی شده است.
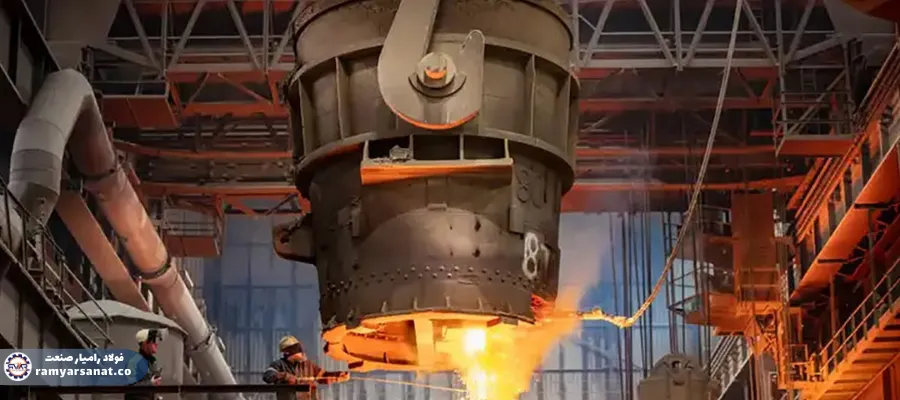
تفاوت کوره القایی و قوس الکتریکی
برای بررسی تفاوت کوره القایی و قوس الکتریکی، آنها را از 4 جهت مورد بررسی قرار میدهیم. در ادامه به فرق کوره القایی و قوس الکتریکی از جنبه های مختلف میپردازیم:
- تفاوت کوره القایی و قوس الکتریکی از نظر تصفیه
یکی از تفاوت های این دو کوره در تولید سرباره گرم و سرد است. کوره القایی سرباره سرد و قوس الکتریکی، گرم میباشد. ضمن اینکه کوره قوسی توانایی بیشتری در حذف فسفر، گوگرد و رفع اکسیداسیون دارد.
- فرق از نظر تصفیه کربن
کوره القایی به اصل گرمایش القایی وابسته است؛ این در حالیست که قوس الکتریکی برای گرم شدن به الکترود سنگی نیاز دارد.
- تفاوت از نظر بازده عناصر آلیاژ
کوره القایی بازده عناصر آلیاژی بالاتری نسبت به کوره قوس دارد. همچنین مقدار سوخت عناصر در کوره القایی کمتر از کوره قوس الکتریکی است.
- متفاوت بودن میزان بهره وری
زمان اتمام فرایند ذوب در کوره قوسی حدود 50 الی 60 دقیقه است؛ در حالی که این فرایند در کوره القایی حدود 120 الی 150 ساعت می باشد.
در پایان
در این مطلب به بررسی تفاوت شمش قوس و القایی به صورت کامل پرداختیم. همانطور که گفتیم این دور روش ضمن مزایا و معایب خاص خود، تفاوت های زیادی نیز با یکدیگر دارند. پیشنهاد میکنیم برای کسب اطلاعات بیشتر در زمینه تولید شمش فولادی، مطلب " روش تولید شمش فولادی " را مطالعه کنید. همچنین می توانید برای اطلاع از قیمت روز آهن آلات، با شماره 03155057 تماس بگیرید.
سوالات متداول
چه عواملی بر کیفیت شمش فولادی تأثیر میگذارند؟
کیفیت شمش فولادی به فاکتورهای مختلفی مانند ترکیب شیمیایی، فرآیند تولید و فناوری ریختهگری بستگی دارد. میزان عناصر موجود در ترکیب شمش، از جمله کربن، گوگرد و فسفر نقش مهمی در استحکام و خواص مکانیکی آن دارد. همچنین روش تولید شمش نیز بر کیفیت آن تأثیرگذار است. شمشهای تولیدشده در کوره قوس الکتریکی معمولاً کیفیت بالاتری دارند، زیرا این فرآیند امکان کنترل دقیقتر ترکیبات و ناخالصیها را فراهم میکند.
چه نوع شمشی در تولید میلگرد استفاده میشود؟
برای تولید میلگردهای با قطر ۱۴ تا ۴۰ میلیمتر، معمولاً از شمشهایی با میزان کربن بین ۳۰ تا ۳۵ درصد استفاده میشود. در حالی که برای مقاطع فولادی با ابعاد کوچکتر، از شمشهایی با درصد کربن پایینتر بهره میبرند.
تفاوت شمش تولیدشده در کوره القایی و قوس الکتریکی چیست؟
شمشهایی که در کوره قوس الکتریکی تولید میشوند، به دلیل یک مرحله آنالیز بیشتر، معمولاً از کیفیت بالاتری برخوردارند. این فرآیند امکان حذف ناخالصیها و کنترل دقیق ترکیبات شیمیایی را فراهم میکند، در حالی که شمشهای تولیدی از کوره القایی ممکن است درصد ناخالصی بیشتری داشته باشند و کیفیت نهایی آنها پایینتر باشد.